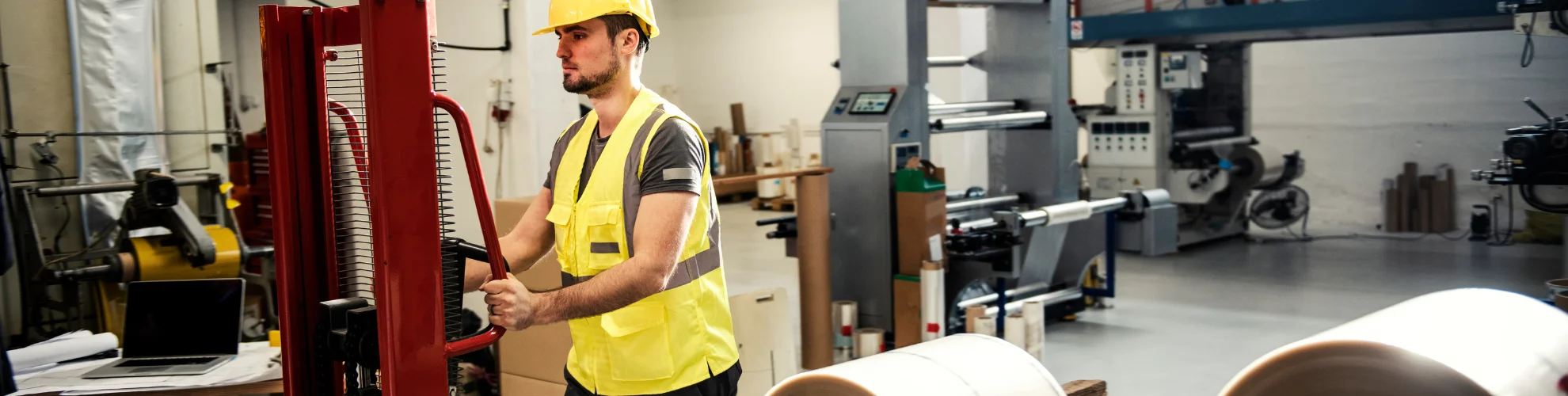
Milk run systems – pros and cons
A milk run logistics system, also known as Mizumashi, is an approach to internal material handling that aims to optimize logistics processes in manufacturing plants. Compared to the conventional use of forklifts, the milk run system offers several advantages.
What is a milkman loop?
The name “milk run” originates from the days when milkmen delivered fresh milk to customers’ homes. The milkman, who had a fixed route, visited the same customers every day, collected empty bottles, and delivered new ones. The route was optimized to maximize time and resources, minimize empty runs, and ensure regular deliveries. In logistics, the term “milk run” refers to a similar concept for optimizing transport routes, in which vehicles collect materials from various suppliers and deliver them regularly and efficiently to a production facility. The goal is to minimize transportation costs, reduce inventory, and ensure timely deliveries, similar to the daily milk delivery by a milkman.
Milk Run vs. Forklifts
Conventional forklifts are particularly useful in warehouses where products are stored vertically. However, in factories where transport between production cells is horizontal and no materials can be stored, the milk run system is a significantly better solution.
Implementing the milk run system instead of the traditional use of forklifts requires appropriate planning and adaptation of logistics processes, but the advantages of this solution can significantly influence the optimization of logistics and production processes.
The main advantages of the Milkrun system include:
Reduction of inventory levels | The milk run system enables more frequent deliveries of smaller quantities of material, which allows for a reduction in inventory levels in the warehouse and on the production line. This makes it possible to reduce storage costs. |
Increased efficiency | Systematic and planned delivery routes enable more efficient use of time and resources, avoiding unnecessary downtime and waiting for materials. |
Better work organization | Thanks to regular and predictable deliveries, production employees have constant access to the materials they need, improving workflows and increasing their efficiency. |
Space optimization | Using a milk run system can contribute to better management of production space, as it reduces the need for large storage space on the production line. |
Reduction of traffic and congestion | Through organized and optimal routes, the milk run system reduces the traffic of forklifts and other vehicles in the factory, which translates into safety and a lower risk of accidents. |
Reduction of energy consumption and emissions | More efficient route planning and delivery planning can lead to lower fuel and energy consumption, which is beneficial from both a cost and environmental perspective. |
Flexibility and scalability | Milk run is easier to adapt and scale to changing production requirements, allowing you to respond quickly to changes in demand. |
Improving Quality | Regular deliveries and smaller quantities of materials delivered directly to the production line can help reduce the risk of damage and improve the overall quality of the materials. |
How can CO2 emissions be reduced with milk run transportation?
Suppose a company has a production facility that traditionally uses forklifts to transport materials from the warehouse to the production line. Switching to a milk run system can help reduce CO2 emissions in several ways.
By switching to the milk run system, you can reduce CO2 emissions by almost 7 tons per year thanks to the lower fuel consumption of the forklifts. This is an example that shows how optimizing logistics processes can not only increase operational efficiency but also reduce the environmental impact.
Assumptions |
|
Traditional transport system |
|
Milkrun system |
|
Reduction in CO2 emissions |
|
Replacing forklifts with a milk run system
Replacing forklifts with milk run trains in production facilities and warehouses is a trend that is becoming increasingly popular due to its numerous advantages. Below is a summary of statistics that illustrate the impact of implementing milk run trains on logistics operations:
- Reduction in operating costs: Average reduction in operating costs associated with internal transport after implementing the Mizumashi system: 20%–40%.
- Reduce CO2 emissions: Estimated reduction in CO2 emissions from using Mizumashi trains compared to forklifts: up to 33%.
- Material flow optimization: Increased material flow efficiency and reduced waiting times for deliveries: by 25%–50%.
- Accident reduction: Reduction in the number of accidents and incidents related to internal transport after implementing the Mizumashi system: up to 50%.
- Improved space utilization: Reduction of warehouse space occupancy through more effective route planning and more frequent deliveries: by 15%–30%.
- Increased operational flexibility: Improved operational flexibility and adaptability to changing production requirements thanks to the modular design of Mizumashi trains.
- Energy efficiency: Reduced fuel and electricity consumption through more efficient and organized internal transportation.
These statistics illustrate how the implementation of a milk run system can bring significant benefits to production facilities and warehouses by improving safety, operational efficiency, and reducing environmental impact. Please note that specific values may vary depending on the specifics of a particular facility, its size, and the degree of implementation of the milk run system.
A Milk Run System for Your Company
This article compares two popular internal transport systems used in factories: forklifts and milk run trains. Both solutions have their advantages and disadvantages, but the analysis recommends milk run trains as a more effective alternative.
Milk run trains are proving to be a more cost-effective option for modern factories looking to optimize internal transport. Thanks to their efficiency and safety, the milk run system can significantly improve production efficiency and reduce operating costs.
To maximize the potential of milk run trains, we recommend running simulations in factories. These simulations allow you to accurately assess the benefits of modernizing your internal transport fleet. We also recommend consulting with Atres experts who can help you analyze and adapt the milk run system to your company’s specific production requirements.